What is CMP slurry?
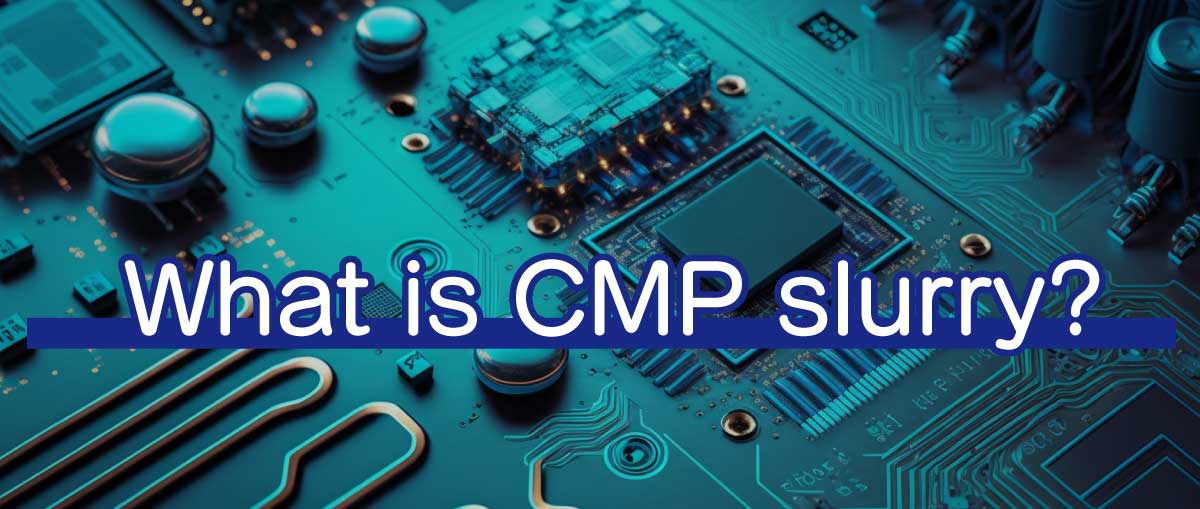
Manufacturing Process
The production of CMP slurry requires dispersion technology. Dispersion technology refers to the technology to mix (disperse) particles uniformly into liquids, etc.
By rapidly rotating stirring blades in a powder-liquid mixture, the shear force of the stirring blades breaks down aggregated particles and disperses them uniformly in the solution. In the case of CMP, when using purchased silica or similar powders as abrasive particles, stirring dispersion prevents particle aggregation and minimizes the generation of scratches.
Polishing methods using CMP slurry
Cu devices consist of an insulating film, copper (Cu) as the wiring metal, and a barrier film (typically Ta) to prevent Cu diffusion into the insulating film. In the first step of the polishing process, Cu is polished using Cu CMP slurry, and the process is stopped at the Ta surface. In the second step, Ta CMP slurry is used to polish both Ta and Cu.
Polishing equipment
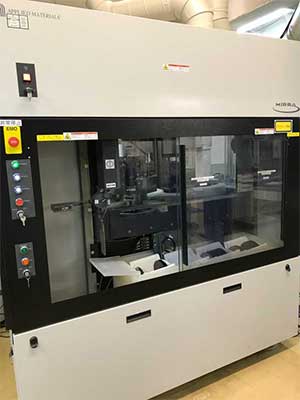
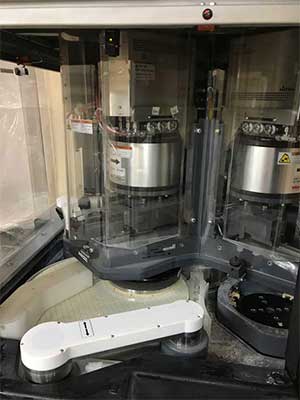
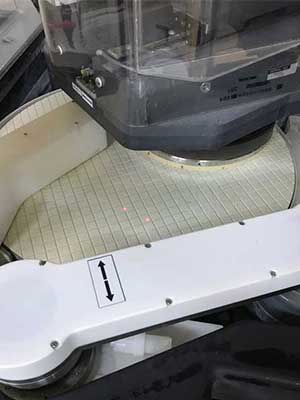
CMP slurry product lineup
We provide various types of CMP slurries.
We are good at polishing dissimilar materials with high or low selectivity, rather than polishing a single material.
Applications |
Product name |
Target material |
Description |
---|---|---|---|
For copper devices and 3D wiring connections |
TPC |
Cu | Silica slurry for copper wiring polishing in semiconductor devices. |
MKT |
Ta | Silica slurry for barrier film polishing in semiconductor devices. | |
MKW |
W | Silica slurry for W contact plug. | |
For TSV |
SE-High <Under development> |
Thick film Cu |
Silica slurry for thick film Cu polishing Cu high-speed removal on the order of microns |
Si-07 <Under development> |
Si | Slurry for polishing the backside of Si substrate and TSV. | |
For resin polishing |
CME <Under development> |
Filler-filled resin-film | Resin polishing slurry for build-up substrate |
PI-01 <Under development> |
PI, Cu | Slurry for polyimide film and copper polishing | |
Others |
CMS <Under development> |
SiO2 | Ceria slurry for semiconductor oxide film polishing |
DS-01 |
Magnetic head (AlTiC) |
Oil-based diamond slurry Good redispersion, achieves high-speed polishing with low scratching Reduction of adherends to the polished object after polishing |
Example of slurry development
We have developed various types of CMP slurries, mostly for metals and ceramics.
Here, we would like to introduce some examples other than those.
[Example: Resin Polishing Slurry]
History
A device manufacturer wanted to polish polyimide (PI) while stopping the polishing when reaching the surface of copper (Cu) plugs embedded in the polyimide. They approached us with this challenge. In addition, the polishing speed requires a micron-order polishing speed per minute, and we received a request to care about the surface roughness. Through polishing tests, we identified the appropriate particle type, particle size, pH, and reaction enhancers, and were able to achieve a good removal rate/Ra ratio, receiving positive evaluations compared to other companies' products. Since we have an evaluation device that can perform evaluation such as level difference measurement while polishing, we have led to such evaluation. Recently, there have been very many inquiries about this polyimide polishing slurry.
Good points
■Good polishing characteristics
・ Composition designs (particle type, particle size, pH, and reaction enhancers) meeting customer requirements
■Evaluation equipments for polishing characteristics
・Step measuring machine, Film thickness measuring machine, AFM
Contract case for slurry manufacturing
If you have any manufacturing concerns, please feel free to contact us.
[Example: Water-based Slurry]
History
A battery materials manufacturer faced the challenge of preventing the contamination of conductive materials during their production process and reached out to us for a solution. The materials used in our manufacturing line consist of stainless steel for metals, with fluororesin layered on top of the metal. Additionally, we use fluororesin as much as possible for the liquid-contact parts. This allows us to minimize the introduction of metals and metal ions. Since we were a manufacturing line that cared for metal contamination, we were able to meet the requirements of the battery material manufacturers. Furthermore, as we manufacture products for the semiconductor industry, we have a track record of manufacturing in cleanroom environments, a well-established quality system, possession of various analytical instruments for property measurements, and most importantly, expertise in particle dispersion. These factors were highly valued, leading to our selection as a manufacturing partner. Although there was a need for rapid production within a short timeframe, we were able to leverage the expertise we have accumulated and quickly establish a production system. Currently, we continue to undertake manufacturing contracts without any quality incidents or delivery delays.
Reason for selection
■Enhanced facility environment
・Production in a cleanroom
・Quality assurance system
・In-house analysis/evaluation
■Years of experience in semiconductor product manufacturing
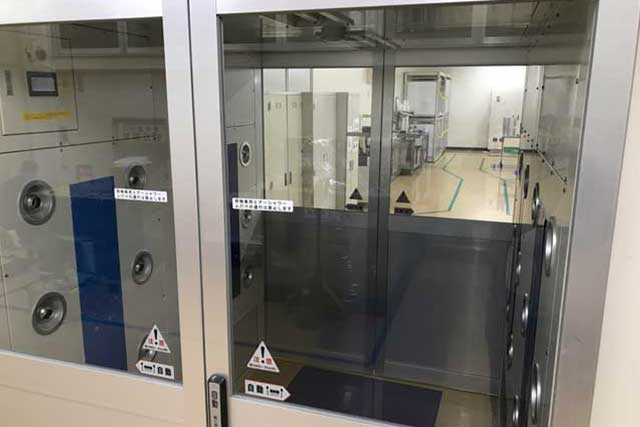
Cleanroom (air shower)
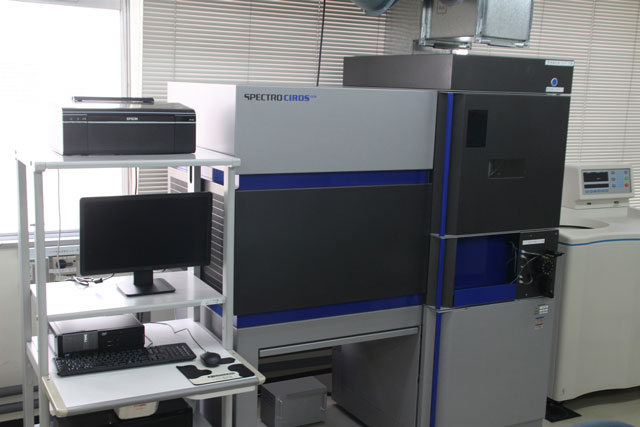
ICP